Wyndham boosts speed and service with AI agents
Wyndham used AI agents to cut brand review time by 94% and boost guest support, scaling smarter across global operations.
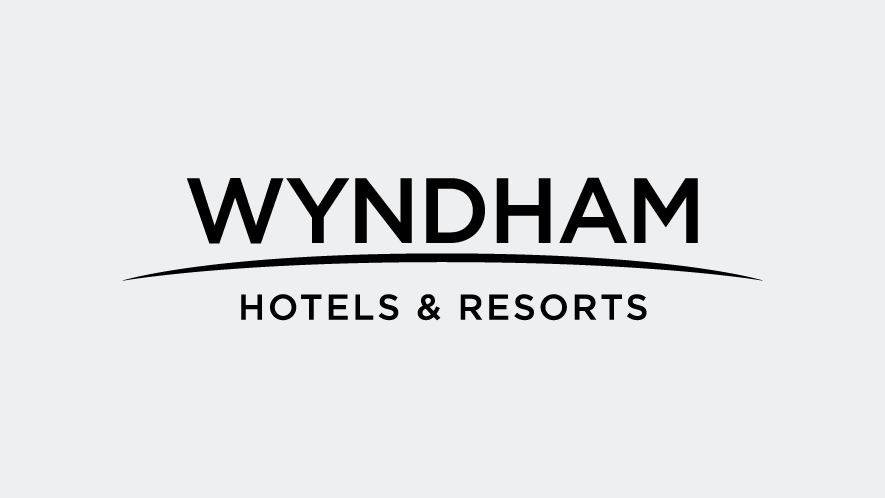
Momentum isn’t just about speed — it’s about impact. We work alongside our clients, combining deep expertise with leading tech so you can break barriers, spark innovation and turn ambition into reality. Our case studies show how we’ve helped businesses go further, faster. Now, let’s create what’s next — together.
Wyndham used AI agents to cut brand review time by 94% and boost guest support, scaling smarter across global operations.
Discover how PwC helped GE split into three industry-leading companies, fueling bold innovation, global efficiency, new growth possibilities and deals transformation.
An enhanced trade promotion management solution with SAP technology and ongoing managed services help Hershey streamline operations and boost revenue.
Bristol Myers Squibb transforms its treasury function through digital automation, achieving pharma industry-leading practices and innovative solutions.
Wyndham used AI agents to cut brand review time by 94% and boost guest support, scaling smarter across global operations.
Regional health system worked with PwC to deploy AI-driven patient engagement, reduce call burden and enhance outcomes with Salesforce Health Cloud.
Discover how PwC helped GE split into three industry-leading companies, fueling bold innovation, global efficiency, new growth possibilities and deals transformation.
Dress for Success and PwC created a nonprofit strategy to amplify impact, grow support and empower women through career development.
BMC modernized its quote-to-revenue process with PwC and Zuora, enabling SaaS growth, new revenue streams and improved customer experiences.
Southwest used GenAI with PwC to modernize its crew management software—cutting planning time in half, reducing costs and accelerating transformation.
INROADS collaborated with PwC to implement Microsoft Fabric, integrating data from six sources for enhanced analytics, streamlined reporting and growth.
PwC, KAYAK & Blockskye transform corporate travel with blockchain, cutting costs, increasing transparency and streamlining booking.
IoT workplace safety wearable technology reduces risks, boosts efficiency, lowers insurance costs, offers real-time hazard monitoring for industrial companies.
Discover how a healthcare provider transformed operations with PwC and Workday, enhancing compliance, boosting effectiveness and optimizing planning.
Happy Ring by Happy Health: FDA-approved wearable smart ring for clinical-grade health data, revolutionizes remote patient monitoring and care.
PwC helped a global insurance company redefine its business model to enter the US market and launch a Salesforce-based platform to support caregivers.